When it comes to high-temperature furnace lining applications, using low bio-persistent fiber (Body...
Galvanize Your Efforts to Eliminate Furnace Heat Loss with Unifrax MX Modules
When it comes to the strength of metals, steel tops them all. Because steel contains iron ore, it tends to rust. For that reason, most low-alloy steel is painted, plated, or treated otherwise to prevent exposure to air and moisture. Galvanizing is an effective, low-cost way to improve steel’s durability while providing a surface finish that accepts paint as an additional layer of protection.
A key player in enhancing furnace efficiency and reducing heat loss in the metal manufacturing process is the Fiberfrax® MX Grade Anchor Loc® Modules. These modules offer an advanced solution for thermal management in high-temperature environments. Their introduction marks a significant step forward in extending furnace life and optimizing energy use, bridging the gap between traditional methods and modern demands for durability and efficiency.
Table of Contents
Introduction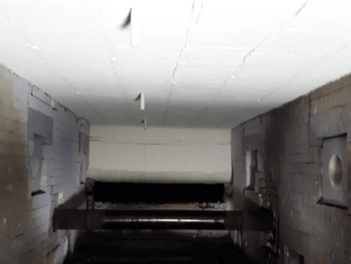
Part of the process for manufacturing galvanized steel consists of using a Non-Oxidizing Furnace (NOF). This type of furnace has a high operating temperature (e.g., 2550oF (1400oC)) and the furnace roof is where most furnace heat loss occurs. These temperatures typically cause issues for traditional 2600 degree modules or require a significant investment for 3000 degree modules. The Unifrax MX module helps to bridge that gap at a much more affordable price.
To minimize heat loss and optimize thermal management, manufacturers of steel and other metals can use Fiberfrax® MX Grade Anchor Loc® Modules. They are thermal-efficient furnace linings made of alumina, zirconia, and silica, and feature ceramic fiber chemistry that is unique to Unifrax.
Fiberfrax MX Grade Anchor-Loc Modules in Action
A typical example of a Fiberfrax MX application consists of a job we recently supplied for a steel manufacturer to line two nosing sections and a back wall of the customer’s furnace. The furnace’s walls are lined with refractory brick.
The lining installed consists of a series of modules that are 1 foot (300mm) thick and edge-stacked at a density of 13 lbs./ft3 . The modules are positioned in a uni-directional manner with a single blanket with a dimension of 1 in. x 8 lbs./ft3 between rows of modules.
During installation, the thickness was compressed to 0.50” , and a layer of Fiberfrax Durablanket SF (aluminum foil faced) that is 0.50” thick was used as a backup layer behind the modules.
The arch area lined is rectangular, measuring 15.5’ long and 6.5’ wide. The modules installed were 1’ square blocks with special L-shaped corner module nosing used in the lining.
The Benefits & What’s Next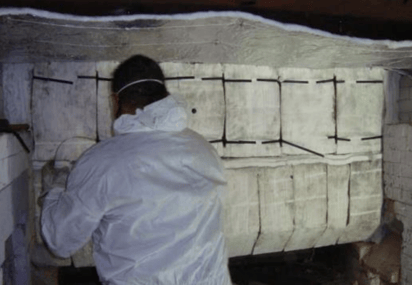
As a result of this installation, which included extensive collaboration with the customer, the furnace is back in service.
Besides being highly satisfied with the quick installation of a proven lining system that combines thermal efficiency with long service life, the customer is looking to replace the brick walls of another furnace with a Unifrax module lining.
As the saying goes, one thing leads to another. For help with your next project requiring high-temperature insulation or refractories…